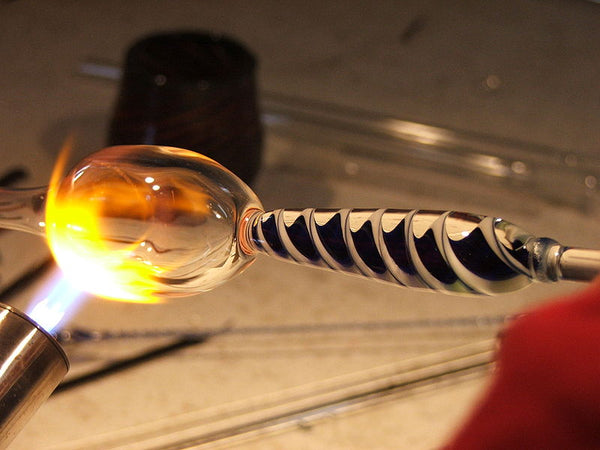
Learn Borosilicate Glass Blowing Art
Glass is one of the most versatile substances on Earth. It can exist in any color and have virtually any texture. Glass can be used for anything from tableware to skyscrapers and everything in between. It's also possible to create just about any shape imaginable with glass.
But glass doesn't grow on trees—that'd be pretty weird. Instead, it forms under particular conditions over long periods. Naturally-occurring glasses like Libyan desert glass are prized for their rarity and beauty.
Because naturally-occurring glasses are relatively hard to find, we figured out how to make borosilicate glass with its own brawn (and some brainpower, too). Let's take a look at the basics of borosilicate glass blowing so you can see firsthand how MJ Arsenal dab rigs come to be.
A Quick History of Glass Blowing
Borosilicate glass blowing is a difficult and delicate art, but it’s been around for centuries. The first glass blowing was done in the Syro-Palestinian region using blowpipes and has since evolved into the challenging but rewarding art of modern glass blowing.
Glassblowing technology proliferated as the Romans built an expansive empire, and people began to use glass in their everyday lives. Populations across Europe, Asia, and North America relied on the glassblowing craft to fashion functional vessels as well as decorative items.
Mass Production of Borosilicate Glass & Applications in Science
The 17th century saw a revolution in science, with the invention of microscope lenses and laboratory glassware. Because of the increased demand, glassmakers were forced to try out new additions for stronger, heat-resistant, or chemical-resistant materials that would not shatter under pressure like previous iterations.
The invention of lead glass in 1676 created a new material that was more durable than its predecessors. Mixing glass with other metals to create a type of glass that would not shatter or corrode was a breakthrough. It resulted in less risk for scientists who used flasks and beakers during experiments, as well as making it easier for them to clean after use.
German scientists and instrument makers in the 1880s worked to create a material they named "borosilicate glass." It had improved properties over other types of laboratory glasses, making it perfect for use with high-temperature or harsh chemicals. It was first branded and marketed under the name "Jena Glass," in the same way that "Pyrex" is used as a proprietary eponym for borosilicate glass today.
Today, glassblowing is still a fairly common profession despite its mass production. Not everyone is born with the natural talent of legendary glassblowers like artist Bob Snodgrass, but glass artisanship is seeing a new boom in the 21st century with the explosion of demand for reliable dabbing and smoking tools.
A lot of different materials have seen their heyday for dabbing—ceramic, silicone, and even titanium. But one material has stood the test of time and continues to lead the market—borosilicate glass.
Different Types of Glass
To the layman’s eye, all glass is, well, just glass. But a craftsman knows: Not all glass is created equal. We rely on different types of glass for specific applications, and the chemistry and structure of each type vary.
For example, soda lime glass was used in windows and beverage bottles (which is probably where it got its name). It’s ideal because it’s inexpensive and easy to melt and shape. However, it also has poor durability and can’t withstand extreme temperatures very well. These limitations contributed to our expansion of glass types.
Let's look at some of the most common types of glass you'll find around your home, as well as in labs and other settings.
#1: Natural vs. Synthetic Glass
Naturally-occurring glass is typically only formed in meteorites or on Earth's surface, like Libyan desert glass, which looks nothing like your typical drinking glasses. Also known as tektites, naturally occurring glasses are made up of high levels of silica (SiO2).
Man-made or synthetic, glass is made when silica combines with other chemicals. The result is a substance that you can mold into various shapes and colors under the right temperatures.
Due to the chemical processes used, artificial glasses tend to be less pure than naturally occurring ones, but they're often easier to find and work with. And when it comes to glass, high purity isn't everything. Synthetic glasses can be just as beautiful and strong as naturally occurring glasses.
Type #2: Borosilicate Glass
Borosilicate glass is one of the most common types of glass used for scientific applications. Since the late 1800s, this type of glass has been used to make scientific laboratory equipment because of its excellent thermal properties.
It has three significant benefits: it's durable, chemically resistant, and thermally shock-resistant. It can be used to make flasks, boiling tubes, condensers, and many other pieces of lab equipment for which soda-lime glass is unsuitable.
Borosilicate glass is also less brittle than traditional soda-lime glass, which means that broken pieces are more likely to stay in one piece rather than shatter into tiny shards of sharp debris.
Today this glass is still widely used to create high-quality laboratory test tubes and other tools for laboratories, research universities, and chemical manufacturing.
And if it's good enough for the lab, it's good enough for a dab.
Borosilicate glassware is the gold standard for dab rigs because of its strength and thermal shock resistance. This durable glass is resistant to rapid temperature changes, so it can take the abuse of repeated heating without cracking or breaking. It’s also a prime choice for creating visually mind-blowing dab rig collections.
Unfortunately, many glass blowers still use less expensive soda-lime glass, which is the same type of glass that drinking and cooking containers are made out of. It has a low melting point and shatters easily when heated or cooled rapidly. It simply won't last as long as high-quality borosilicate glass when used for dabbing.
Type #3: Soda-Lime Glass
Soda-lime is a soft glass that's typically used for everyday household items, such as jars, drinking glasses, ovenware, or even shower doors. It can also be used to make less expensive laboratory glassware that's not subject to the same degree of thermal stress as borosilicate glass products.
This glass is made by melting sand together with soda ash (sodium carbonate) and limestone (calcium carbonate). It has a very low melting point, making it easy to manipulate. It can be formed into any shape or size, which makes it inexpensive and popular for use in the home.
However, soda-lime glass doesn't make for very good dabware.
Though it’s inexpensive, soda-lime glassware is low in quality. That means it can be weakened or even destroyed when heated too quickly or cooled too rapidly. This type of glass won’t typically hold up during the repeated heating and cooling cycles that are necessary for dabbing. In fact, this lack of thermal shock resistance is the most common reason that cheap glassware breaks—besides just physical impact.
High-quality borosilicate glass, on the other hand, has excellent thermal properties. It's more durable and resistant to impact than soda-lime glass, so it can stand up to being heated and cooled repeatedly without cracking or breaking.
Type #4: Quartz Glass
Quartz is a naturally occurring substance, but quartz glass is man-made from quartz dust and sand. Quartz glass is nearly pure silica—95% or more—but this formulation makes it difficult to work with and very expensive to manufacture.
Because it's so expensive, quartz glass is only used when durability and clarity are critical. You’ll find it in high-end optics in microscopes, telescopes, watches, and even aerospace manufacturing.
And at MJ Arsenal, we also use it to mold our premium quartz bangers and buckets. Its extreme heat retention makes it ideal for dabbing, and quartz is naturally resistant to heat degradation.
Hand-in-hand with borosilicate glass, quartz is quickly becoming the standard for high-quality dab rigs. It's easy to see why—quartz glass has superior heat retention properties and is more durable than soda-lime glass.
But unlike borosilicate, quartz is also more expensive to manufacture. So when it comes to the base and body of your rig—which you aren't firing with your torch—borosilicate glass is still the way to go.
Less Common Glass Types
Glass comes in other formulations, too. Some examples include:
Aluminosilicate Glass
Aluminosilicate is similar to borosilicate glass in that it is resistant to high temperatures. It's more impact-resistant than borosilicate, but it's much less pliable. As a result, it's often found in flat panel shapes like stove top surfaces.
Furthermore, aluminosilicate glass is expensive to produce and difficult to work with, making it impractical for smoking and dabbing. Borosilicate glass is nearly a century-old technology, meaning it's become very affordable to manufacture. Combined with an efficient design, this lets us build dab rigs that are functional, durable, and inexpensive all at the same time.
Lead Crystal
Lead crystal glass is typically made with lead oxide (PbO). This gives it high transparency but also makes it more expensive and fragile. Because of its lead composition, it’s also unsuitable for use in drinkware or other consumable applications.
There's simply no valid reason to use lead crystal dab rigs, nor is there ever likely to be. Not only are they expensive and impractical, but they're not safe for dabbing. Borosilicate is clean, clear glass—and it's easy for glassmakers to decorate it with colored rods and frit. So there's no need to risk your health with a lead crystal dab rig when you can have the best of both worlds with borosilicate.
It's worth noting that if you buy from a glassmaker that doesn't disclose what type of glass is used in their dab rigs, you can't be sure what you're getting.
While borosilicate is by far the most common glass type for dab rigs today, that's not always the case. It's well within reason that other types of glass might be used—even lead crystal—so it pays to do your homework and ask questions before buying.
Polycarbonate Glass
Polycarbonate glass is a tough, transparent material that's often used to make safety glass. It offers more impact resistance than other types of glass.
Many of us have probably seen polycarbonate glasses before, but they are most often found in protective eyewear or shatter-resistant sunglasses. This type of glass is nearly impossible to break with an everyday drop—but despite its toughness, it has a surprisingly low COE.
Heating up polycarbonate glass to dabbing temperatures softens it enough to cause it to warp and deform. It can even be molded at near-room temperature if it's been heated up enough to start melting.
Borosilicate glass might not stop bullets, but even if you're taking your dab rig to war, it won't do you any good if it softens under extreme heat. Borosilicate glass offers the best durability you can get in a piece of heat-resistant glass.
Ultraviolet
Ultraviolet glass is clear quartz glass that has been specially treated with magnesium fluoride to block UV light. This glass can be used in fluorescence applications where UV light would damage or adversely affect the experiment.
What's neat about UV glass is that it glows under UV light, so you can still enjoy your rig even when it's dark outside. It makes beautiful decorative accents, like our limited edition Rigloo holiday dab rig and our Apollo Series (in collaboration with Northstar Glassworks).
Glass Blowing Terms to Know
There are a lot of funny words in glass blowing that people use to describe the different pieces of hardware used during the process. Here are a few of the most important terms to know before you go shopping.
- Glass blowing: A type of glass artistry that involves manipulating molten or softened glass with tools, including blowing and sculpting the material into the desired shape.
- Lampworking: A type of glass blowing that uses a small, handheld torch instead of a furnace. Thomas Grimmet at Glass Alchemy breaks down how the process works.
- Gather: To form a piece of molten glass around a rod (the gather stick) for manipulation during the process.
- Head: A piece of metal at the end of the blowpipe that's heated for shaping glass.
- COE: Stands for "coefficient of expansion." Once the glass has been heated, it changes shape as its temperature fluctuates. COE is a measure of how much the glass expands or contracts with changing temperatures. The greater the number, the more malleable and workable the glass is.
Free-Blowing vs. Mold-Blowing
The first way to blow glass is the free-blowing method. With this technique, you are working with molten glass gathered on a metal pipe and heated in the furnace. You then roll it out into a long cylinder by rolling it against the edge of your bench.
You then take this mass of hot, molten glass and shape it into traditional objects, like bowls or vases. Generally, you keep adding glass to these blown pieces by gathering more glass onto the end of your blowing pipe or rod while simultaneously twisting and shaping what you already have.
The other method is called mold-blowing, where an artist forms a small ball of solid glass (a gather) on the end of a punty. They dip the mass of glass into a mold and blow air into it to inflate to the desired size.
Both methods are used for creating all kinds of glass pieces. Borosilicate glass is moldable when heated, so it's feasible to make batches of unique shapes like carb caps.
On the other hand, molding extremely small pieces of glass can be tricky, so it's sometimes easier to free-blow pieces like terp pearls. The narrow connections and tubes on a dab rig may also be finished by hand rather than mold-blown to ensure the seams are tight and there are no weak points.
How Glass Blowers Shape Glass and Color
The way a glassblower shapes glass is pretty simple. They heat the end of the pipe and then use their hands to stretch it out into a long, tubular piece.
They can flatten or bend this glass tube at will simply by heating and applying pressure with their tools. As pieces are snipped away, a flame is applied to smooth over the rough edges in a process called fire-polishing.
Once they warm the widened glass tubing enough, they can roll it lengthwise into a thinner tube. The glass has to be pretty hot (upwards of 1500 degrees) for this to work correctly.
The glassblower then takes this thin, long tube and blows it up into a bubble. After the blowing portion is complete, they use their tools to ensure the hot glass is uniform and smooth.
Once the glass has gone through the initial shaping process, it's time to start playing with colors. This is done by adding rods of colored glass (called stringer) before shaping it into whatever final product is desired.
Conclusion
Glass art is one of the most stunningly beautiful and collaborative forms of visual art. And glass making is perhaps the most celebrated aspect of smoking culture, which is why MJ Arsenal is so passionate about it.
Our mini dab rigs are just one example of the popular borosilicate glass art made by master artists in America right now. These tiny works of functional art represent an entire artistic movement, and we're stoked to be a part of it.
We have tons of hand-blown glass accessories for sale in our store, so take a look at the selection to see if anything catches your eye. We also love to see people's collections of glass art through social media, so tag us on Twitter @MJArsenal420 to show us your new gear!